The warm spring sun reflected brilliantly off the freshly varnished woodwork as Jack Preston guided his brand new blue and white “Commander” into the fuel dock at Cuttle Marine. As the gas attendant assisted with the lines he gave the boat a thorough once-over before remarking, “That’s a beautiful new Lyman you have there sir.” Jack, slightly surprised at the comment, responded, “It’s not a Lyman”. Caught off-guard by his error the pump jockey quickly recovered and announced, with some authority, that it must be one of the new Chris-Crafts that he had been reading about. Chuckling to himself Jack proudly informed the young lad that, “No son, it’s a Cliffe Craft, and it was built right here in Gananoque”. And so another case of mistaken marine identity was resolved and the name Cliffe Craft became known to yet another resident of the Thousand Islands.
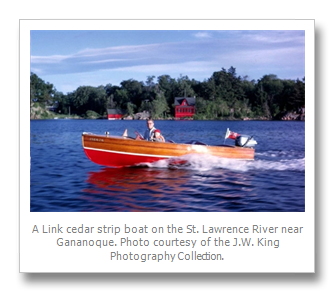
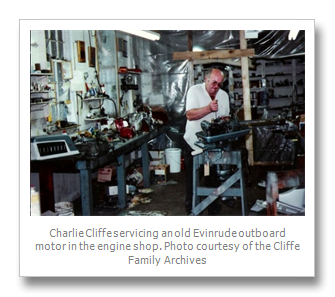
Charlie Cliffe began building boats in the basement of the family farmhouse in Wilstead, Ontario when he was a teenager. He followed his passion for boat building by getting a job with the Link Manufacturing Company in Gananoque after he graduated from High School in 1947. He started out in the mill room, producing the planking and ribs for the cedar strip boats that were being turned out at a rate of 20 – 25 per week. The cedar arrived at the factory in rail cars from British Columbia and, after going through the sawing operation, was transformed into planking with the aid of a four sided planer. The finished dimensions of the planks had to be held to within a couple thousands of an inch of the specified size so it was imperative that the planing equipment was properly set-up and constantly checked. Charlie also milled the B.C.–sourced Sitka spruce planks into material for the boat’s floorboards, as well as the Pennsylvania white oak that was used for the ribs. Once he became fully trained on the milling equipment, Charlie and the sawyer, Howard “Whiz” Matthews, worked through many boxcar loads of timber to produce the various components required for the production of the Link cedar strip boats.
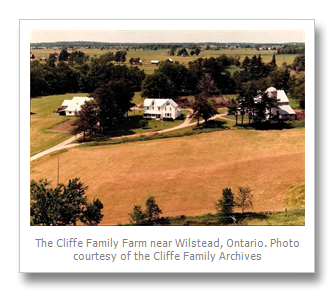
Due to the rapidly declining sales of the Link Trainer, a widely used flight simulator developed by Edwin Link, after the end of World War II the Link Manufacturing Company was forced to diversify the products that it manufactured at the Gananoque factory. Since Mr. Link was an avid outdoorsman, and with the plant being located in the heart of the Thousand Islands, it seemed that boat building was one logical endeavour to pursue.
Along with the innovative “Linkanoe”, and other associated sectional crafts, the company also produced a line of cedar strip runabouts. The twelve foot “Carcarry” and the fifteen foot “Heron” models proved to be more successful than the “Linkanoe”, which ended production after a two year run due to weak sales. By the early 1950’s Link Manufacturing decided to abandon the boat building business altogether and used the manufacturing equipment in the Gananoque facility to produce wooden school furniture instead. At that time Charlie Cliffe struck a deal with Link Manufacturing to purchase the moulds for the cedar strip boat models for a sum of $500. Also included in the deal were the parts and materials for approximately ten boats along with orders for a few boats that still needed to be filled. The moulds were moved to the Cliffe family farm in Wilstead where Charlie, with the help of Jack Gray, a local fishing guide and woodworker, began building cedar strip boats once again.
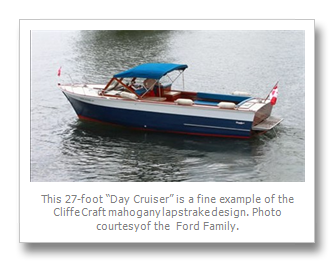
Charlie continued to work at Link Manufacturing for a couple of years after he began the boat business at the farm but eventually found that the new venture required his full-time attention so he left his factory job. It wasn’t long before Charlie and Jack started to develop new models of boats, using the mahogany lapstrake hull design instead of cedar strip. Moulds were designed and built to produce the new style of boats and this marked the true birth of the “Cliffe Craft” brand. Several models of the lapstrake design were developed and built at the farm, including the popular “Commander” model. Cliffe Craft was also a pioneer in the industry by being one of the first builders to install stern drives, built by Eaton, in their boats. A network of dealerships was established in Montreal, Toronto, Brockville, Kingston and the Rideau area, as well as others, to market and sell the Cliffe Craft boats.
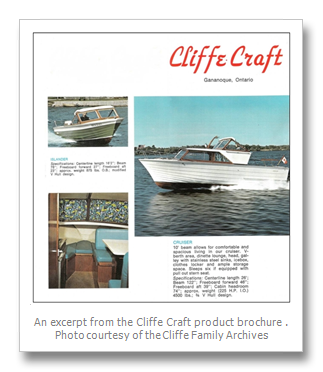
In 1960 Link Manufacturing decided to close the Gananoque factory so Charlie and Joe MacDonald, a long-time Link employee and now business partner in Cliffe Craft, travelled to Binghamton, N.Y. for a meeting with Mr. Link to discuss buying the facility. Link was very receptive to the idea and the sale of the property went ahead. It wasn’t too long after this that all of the boat building equipment and moulds were moved from the farm to the new Cliffe Craft factory. Joe’s wife, Ruth, worked as the office manager and also looked after the accounting duties. Another long-time Link employee, Jerry Kidd, also took an interest in what Charlie and Joe were doing and joined them in the business. Jerry’s extensive background and experience in the design and building of the original Link boats proved to be a valuable asset for the growing company.
The move to the Gananoque factory gave Cliffe Craft the much needed manufacturing floor space and facilities to develop and build larger boats alongside the smaller ones that they were already producing at higher volumes than at the farm. Charlie was also able to incorporate several clever boat construction methods that he had observed at other high-volume production facilities in the States that helped to improve the efficiency of the Gananoque operation.
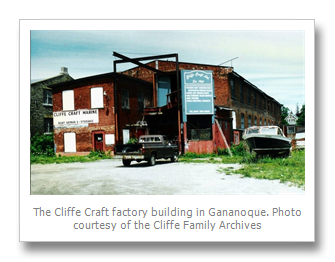
When Charlie Cliffe went about designing and building a new model boat he didn’t have modern conveniences such as computer-aided design software and numerically controlled milling equipment to help make the job easier. The original design ideas were formulated in his mind and were captured on paper in notes and sketches. Once the “vision” was finalized a wooden model, usually in a scale of one inch equals one foot, was hand carved to represent the size and shape of the boat to be produced. After he finished “tweaking” the model Charlie would transfer the measurements to a full-scale shop drawing that would then be used to build the mould for the new boat. The mould was designed and built with jigs and fixtures incorporated into it to locate and hold the critical structural elements of the boat in place during the manufacturing process and to provide consistent size and shape for each of the boats built off of it.
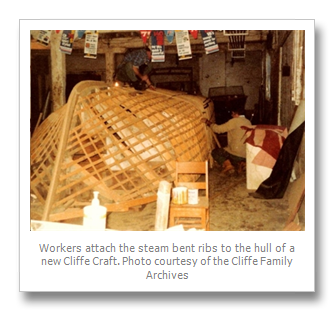
Whether they were building a 16 foot “Islander” or a 26 foot “Cruiser” the manufacturing process was essentially the same for all the boats that Cliffe Craft produced. Charlie and his team of skilled craftsmen included employees Howard “Whiz” Matthews, Les Cook, Bernard “Bun” Ivey, Ronnie Wyborn and David Mabee to name a few. They worked diligently to produce high quality boats to satisfy the strong customer demand.
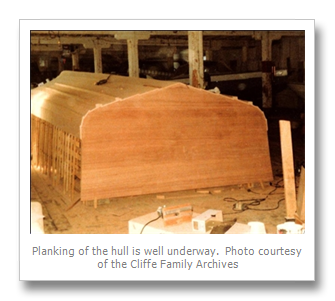
The first steps in the process were to lay the pre-built keelson assembly into the mould and then attach the stem and inner keel to it. The transom was then installed on the mould in the correct location. Following this step, the oak ribs were steamed and bent to shape and then attached to the keelson and inner keel with bronze ring nails. Once all of the ribs were fastened in place the main keel was installed. At this point, the hull was ready to be planked. All of the surfaces where the planking was to be attached to the framing had to be checked and “faired” to the correct shape using a spoke shave to ensure that it fit correctly. Starting with the “number one” plank along the keel, each of the planks was fastened to the ribs with brass screws while the laps were bolted to the ribs with stainless steel bolts. A waterproof sealant was applied to all of the joints where there were any overlaps and where the planks and laps met the transom and stem. The ends of all the planks and laps were then planed off along both the stem and keel to produce a nice line in preparation for the installation of the outer keel. The outer stem was then steam bent and fitted so that it covered the edges of the planking at the bow. At the stern, all of the planks were trimmed off even with the transom and sanded to a smooth finish.

After the final trimming was completed all of the countersunk nail and screw holes were filled with compound and the entire outer surface was sanded. Once the hull was finished up to the gunwales, or the sheer line, it was removed from the mould. After removal from the mould all of the inner surfaces were coated with a preservative to provide protection against rot. The next steps involved installing the deck beams and the decking and fastening the floor bracing. Once these components were installed all of the painting and varnishing was completed. It wasn’t uncommon for Ken Hawkins, the head painter, to have to warm his varnish in a pot of hot water during the cold winter months so that it would flow smoothly enough to give the desired finish. Cliffe Craft offered several colour combinations for their boats but the most popular were red and white, green and white, blue and white, and all white. Following the painting stage the floors were installed and the vinyl deck coverings were applied. Next, the cleats, lights, and other assorted pieces of hardware were installed on the boat. The mahogany windshields, which were also built by Cliffe Craft, were next on the list. Motive power, whether it be stern drive or outboard, was placed in the boat at this point, along with the associated controls and steering equipment. The finishing touches included the installation of the seat cushions, which were also made in-house, and the fitting of the convertible tops, which were purchased from an outside supplier. After a final inspection the newly constructed Cliffe Craft was ready for delivery.
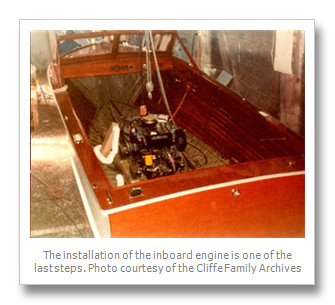
In 1972 the company underwent a significant management change when Joe MacDonald decided to sell his shares and pursue other interests. Tom Conner, a Gananoque native who had moved to Barrie to pursue a career with General Electric, purchased Joe’s shares and joined Charlie as a partner. Although Tom had no boat building experience when he joined Cliffe Craft his engineering background and knowledge of the Thousand Islands area allowed him to get up to speed quickly and he was soon involved in the day-to-day operations. At that time fibreglass boats were beginning to make inroads in the recreational boat market and Cliffe Craft’s wooden boat sales, especially in the smaller sizes, were declining. To try and stave off the economic pressures caused by the market shift Cliffe Craft expanded the products that they offered by becoming a dealer for Crestliner aluminum boats and Thundercraft sports boats, in addition to being an OMC engine dealership. The service work for the OMC engines also became an important source of revenue for the company with Charlie and George Griffin being the primary mechanics.
Through the 1970’s and into the 1980’s Cliffe Craft became more of a custom boat manufacturer, building to order rather than to stock, with their large twenty-five foot twin engine runabout being a strong seller. The boat’s three-quarter V hull, ten foot beam, and spacious layout made it a popular craft for “big” water usage where its’ size and shape could handle rough water. Unfortunately, by 1984 the recreational boating market had turned its’ back on wooden boats and Cliffe Craft ceased production of their mahogany lapstrake designs.

The company did take a brief foray into the manufacturing of fibreglass boats. Cliffe Craft purchased a mould for a fifteen-foot whaler type craft from Penn Yann and built approximately fifteen prototype models. Although the boats turned out well, the design wasn’t big enough for the river and it faced stiff competition in the marketplace. The final nail in the coffin came from the insurance companies who demanded many costly modifications to the factory to mitigate the risks, real or perceived, associated with the fibreglass manufacturing process. Faced with the prospect of having to comply with the stringent insurance regulations the company decided to abandon the fibreglass boat business. After Cliffe Craft stopped building new boats the company concentrated on doing repairs and restorations of wooden boats at the factory. They also manufactured paddles as another means of generating income.
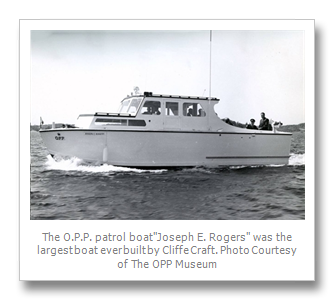
In 1996 a new venture was started – the production of wooden reels for the wire cable industry. With the expertise and equipment available at the Gananoque plant, Cliffe-Craft was able to convince NorCom in Kingston that they would be a viable supplier of reels. With these orders in hand, the company secured bank financing to grow the business. Although the NorCom sales accounted for almost seventy percent of the company’s business in the early years they have since broadened their customer base significantly and are still operating today as GanReel Mfg. Inc. Tom Conner and his son Jeff operated the reel business after Charlie retired.
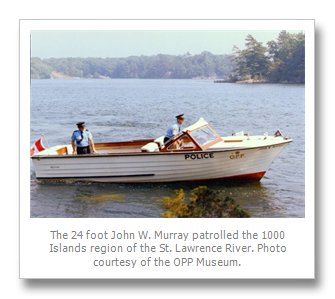
While Cliffe Craft literally built hundreds of boats over the years, there were a few that stood out as being more memorable than others. One of these was the “Joseph E. Rogers”, a thirty-five foot patrol boat commissioned by the Ontario Provincial Police for work in the Georgian Bay area. While it was the largest boat built by Cliffe Craft, it was also one of the few boats not designed entirely by Charlie Cliffe. This particular craft had a deep “V”, smooth skin, double planked mahogany bottom hull design in order to meet the demanding specifications of the Provincial Police. The plans for the cruiser were penned by Clifford Hunt of Rockport who was also a well known builder of wooden tour boats in the area. The Joseph E. Rogers was fitted with twin Chrysler 300 horsepower V8-inboard engines with “velvet” drive, one of only a handful of boats built by Cliffe Craft with this engine configuration. The boat has been retired from police service but is reportedly still operating in the Toronto area under private ownership.
For me personally the Cliffe Craft that stands out in my memory is the “John W. Murray’, another O.P.P. boat that patrolled the waters of the Thousand Islands during the late 60’s and 70’s. Although it was a standard twenty-four foot Cliffe Craft design, the bright white paint job with the O.P.P. insignia and the word “POLICE” emblazoned on the sides made it very recognizable. Named after the first permanent detective appointed by the O.P.P., the “Murray” was taken out of retirement and returned to Cliffe Craft for a complete restoration in 1999. While the original boat is estimated to have taken between 600 and 700 hours to build in 1968 Mr. Cliffe figures that it took just as many hours to complete the restoration. The “John W. Murray” was used by the O.P.P. as a display boat after the restoration on the Boat and Cottage Show circuit.
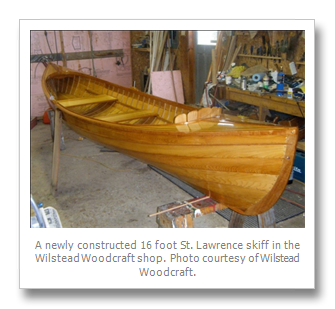
Although Charlie is supposed to be “retired” he is still very active in the boat building business. He and his wife Mollie operate Wilstead Woodcraft, a small family business that hand crafts beautiful cedar strip St. Lawrence skiffs in sixteen and eighteen foot models. Their small shop is just around the corner from the family farm where Charlie got his start in the business. Each boat is a true work of art and they are produced in very limited numbers due to the extensive amount of time and labour involved. In addition to building skiffs Charlie also has a few classic wooden boat restoration projects on the go at any one time. From what I observed, Charlie doesn’t have any plans to slow down significantly in the near future!
Acknowledgements
I would like to recognize and thank the following people who provided assistance with the preparation of this article;
1. Tom McCloud, co-author of the article “Ed Link and his Linkanoe” published in Wooden Canoe” (Aug. 2010 issue 160 vol. 33 No. 4), the journal of the Wooden Canoe Heritage Association, Ltd. The article provided some good background information on the Link Manufacturing Company.
2. Doug and Brenda Dawson, owners of the “Boating with Dawsons” website where they have the “World’s most complete library of old boat brochures”. Doug and Brenda donated two scanned Cliffe Craft brochures from the mid 1960’s as research material for the article.
3. Christine Johnstone, the curator of the OPP museum in Orillia for allowing me to use the two images of the OPP patrol boats built by Cliffe Craft.
4. Heather Ford, for allowing me to use a photograph of the family’s Cliffe Craft boat from their on-line “For Sale” listing. http://www.ladyben.com/SearchResultsFull.asp?VesselID=3369
5. Tom Conner, former partner in Cliffe Craft, for taking the time to sit with me for an interview to gather some historical background on the company, especially the wooden reel business.
6. Charlie and Mollie Cliffe, who provided much of the historical background information for the article as well as sharing many photographs from the Cliffe Family Archives. I also really appreciated the chance to see the Wilstead Woodcraft shop and visiting the Cliffe family farm to check out the classic wooden boat restorations that Charlie is currently working on. Without Charlie and Mollie’s extensive assistance this article would never have been completed.
|
By Tom King
Tom King and his wife Marion, have lived in Milton, Ontario for the past twenty-five years, where they both worked and raised their family of three children; Kris, Mike and Becca. Tom still has a strong attachment to the Thousand Islands, having grown up in Gananoque and being a “river rat” from a very early age. The family tries to return to the islands every summer and for the past few years have been renting a cottage on Sampson (a.k.a. Heritage) Island, just out from Gananoque. This is the sixth article Tom has written for TI Life.
Editor’s Note: Tom King and I want to invite you to share your stories about a Cliffe Craft you may have owned. If you have photos do send them to us at susansmith@thousandislandslife.com we will add them to the article in a slide show.